Unleashing the Potential of wood.
The production of finest veneers is the most decorative and at the same time most resource-saving way of producing high quality, genuine wood surfaces.
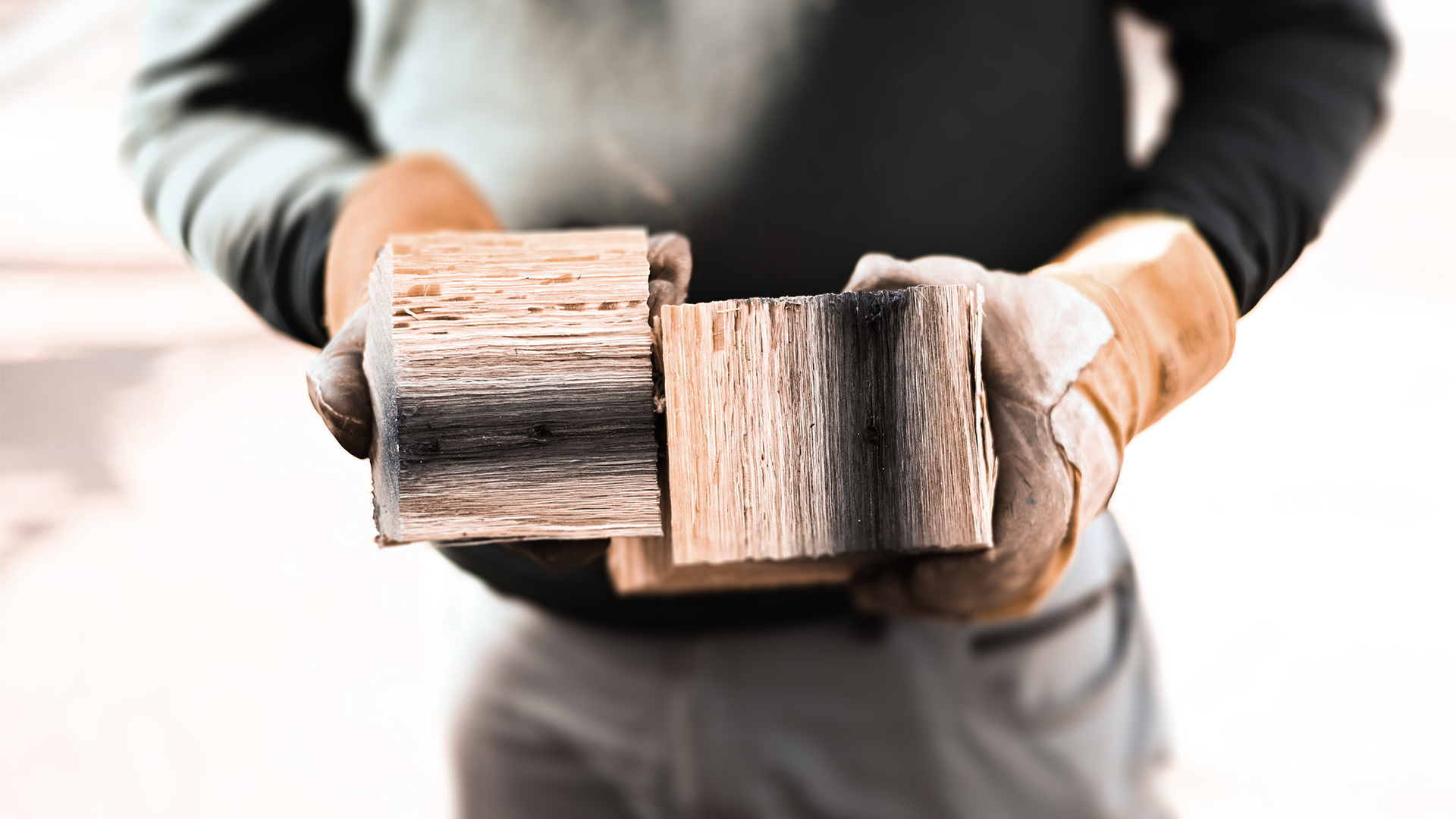
To summarize, the following main reasons are given as to why the production of veneer should be given preference over other comparable woodworking methods:
- Growth, texture and grain of the log can be optimally adapted to the production process.
- Unlimited design possibilities are given during initial production and subsequent usage of the veneer.
- Raw material lumber is used to its maximum extent quantity-wise, natural resources are saved.
veneer manufacturing
Modern veneer production makes it possible to unfold the wood’s creative potential to its full beauty. Through precise procedures such as slicing or peeling wood into thin veneer sheets, maximum use is made of the valuable raw material, which is not only ecologically but also economically important. In comparison to solid wood, up to 50 times more unique and natural surfaces can be achieved.
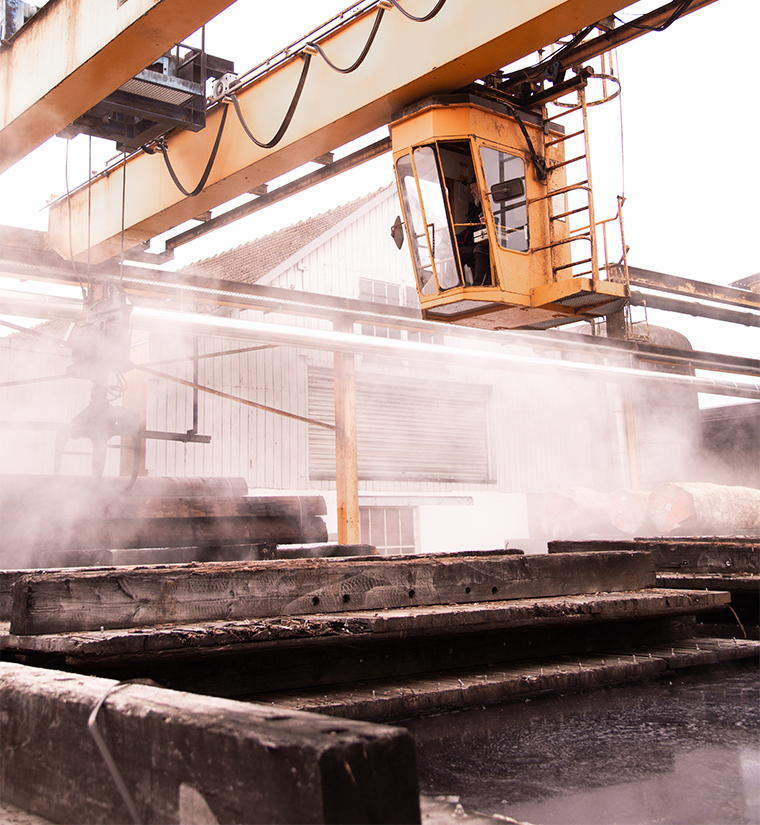
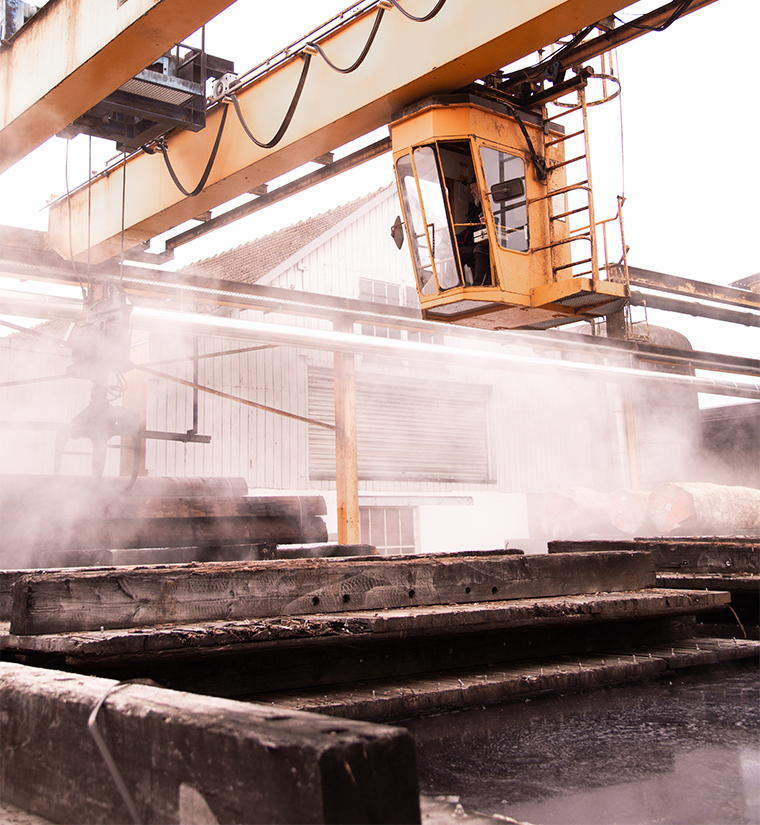
This resource-saving technology opens up almost unlimited design options and perfectly brings out the natural beauty of wood – with all its colours, textures and grains. Each veneer sheet is a unicum, reflecting the unique character of the wood.
Get to know more about the fascinating process of veneer production and how we get the best out of nature.
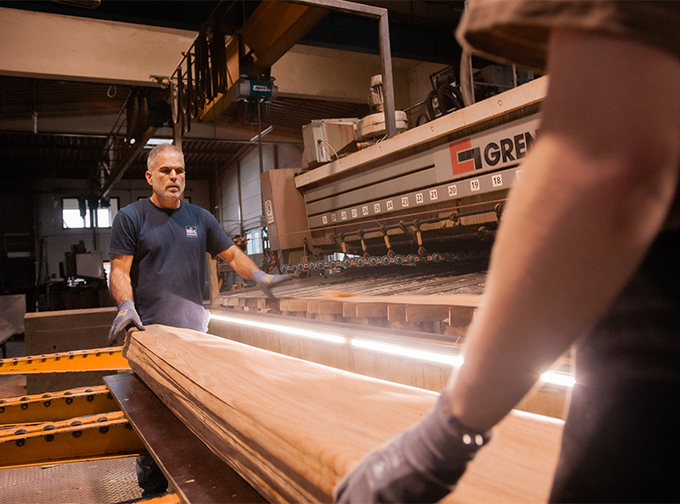
The working up of the veneer logs depends on the following factors, which have to already be assessed in the round log form: Straightness, Heart and tension cracking, Visible faults (knots, pin-knots, decay), Dimension, Color, Texture, Shape
To meet present day quality standards, a veneer surface as far as possible free of defects, uniformly colored and evenly textured shall be achieved. This means that many years of experience and knowledge of veneer are needed to ensure correct, optimal preparation.
There are various methods of slicing which give different surface effects to the veneer. Thorough and skillful assessment of the log with due consideration to the prospectively achievable quality and possible usage thus are the essential basis for the quality of the veneer achieved in its further processing.
After debarking, the veneer flitch is cut on the band saw depending on its preparatory indications; afterwards the single flitches are being cooked.
After the preparation of the flitches, they are being cooked. Exceptions are only species such as Sycamore or White Beech for example, where preferably light or (almost) white coloring is desired. Two effects are achieved by cooking in hot water:
- The wood is given the necessary suppleness to ensure smooth slicing and thus perfect quality in production.
- The color of the produced veneer is influenced by the cooking time. For example, the color of original White Beech is changed by cooking to a pink or salmon-colored hue.
Depending on the species of wood and color demands, cooking periods vary from one day to one week. An individual temperature profile is given for every single species of wood for the respective cooking period. This profile has to be controlled precisely to avoid color defects.
Also the local water quality (hardness, chemical composition) has considerable impact on the course of the cooking operation. That is why individual time and temperature curves have to be empirically calculated for each production site, which need to be met meticulously.
Here at the latest the wheat is separated from the chaff. Where hard material is sliced into finest sheets with tremendous pressure, one does not only need heavy machinery but especially experienced staff who ensure the highest precision with full concentration and dedication.
For the actual slicing operation, the flitches are planed on one or both sides to ensure that the flitch lies perfectly flat on the slicing bed.
Differentiation is generally made between two types of veneer slicing machines:
- Slicing machine for horizontal or vertical cutting
- Peeling machine for rotary cutting, eccentric peeling or stay-log peeling
Different veneer pictures are achieved depending on the machine and slicing method used.
Of decisive importance are exact knife and pressure bar settings to an accuracy of 0.1 mm. This is the only way to ensure perfect quality veneers. It goes without saying that the knife always has to have an extreme sharpness and needs to be reground respectively often, depending on the veneer thickness (and, depending on the species, in different grinding angles.)
On modern slicing and peeling machines, the extremely heavy knife is additionally heated, so that the water exuding during slicing operation vaporizes as quickly and uniformly as possible to avoid condensate marks and blue stain. Other possible slicing defects:
- Scratches: Fine knots (for example in Sycamore), contamination in or on the trunk (grains of sand, little stones) or ingrown metal in the wood (nails, bullets etc.) will chip the cutting edge of the knife and thus cause scratch marks in the veneer leaf. Such chips are either groundout manually or the knife will have to be changed depending on the depth of the chip.
- Deviating thicknesses: These occur as a result of the log being clamped wrongly in the machine or wrong setting of the pressure bar. Another cause is the flitch not lying perfectly flat on the slicing bed.
- Chatter marks: Regular ribs of different thickness, which run across part of the veneer sheet. Causes are the same as those mentioned under “deviating thicknesses”.
Apart from veined wood, the structuring growth rings are always located relatively concentric. Would you now slice a log simply lengthways, it would result in very different veneer pictures throughout the parcel, which is not wanted. Therefore, the log is divided into flitches during preparation, in order to receive preferably homogenous veneer pictures throughout the entire log.
These flitches (exception: rotary cutting) are being mechanically or by vacuum suction attached to the slicing bar, which moves parallel – vertically or horizontal – along the fixed knife. On peeling or stay-log machines, the slicing bar rotates around its axis along the tangential carried knife.
The veneer sheets, still damp from the slicing, are being transported quickly to a modern jet drier, which also has a gentle flattening effect. Every single veneer sheet – supported by suction devices – is inserted by hand and also manually taken out at the end of the drying route. They are then made up into bundles of 24 or 32 sheets each in order to facilitate handling in the warehouse later on. Damaged sheets are already sorted out at this point.
From one wood species to the next different drying programs must be run with regard to belt speed and temperature, which have to be strictly adhered to. Veneer, which is too dry, is brittle and no longer workable. On the other hand, veneers that are too moist can become moldy, thus being no longer usable. A final moisture content of approx. 10-14% is considered to be the average value as a result of correct drying.
Since many veneers tend to buckle after drying due to the different densities given in the veneer leaf, these veneers had to be flattened in the past by means of an extensive additional pressing operation. Meanwhile a press dryer has been developed which gently presses as well as dries the veneer. However, this is only suitable for slightly buckled veneers. Veneers, which are severely buckled (as occurs in Beech), have to be pressed manually again, so that they can be processed further without any problems.
Hardly anyone can and wants to work up veneers with rough edges and nobody wants to pay for more square meters than they can actually use. Therefore, the veneers are clipped on hydraulic veneer clippers into preferably rectangular dimensions.
At the same time, crack formation and other defects, which occur more often in the edge area, are being removed and then the veneers are being made up into bundles of 24 or 32 sheets each, before they are being graded.
After the veneers have run through the entire production process they not only have to be costed, which means that they have to be evaluated and priced, but they are also graded into different qualities. Here, all parameters are imported in our merchandise management system and administered electronically – with an inventory of averagely 8,000,000 sqm veneer and 5,500 cbm lumber, it would else be a monumental task to find just the right veneer for you.
Generally, a difference is made between: Interior architecture quality, Bedroom quality, Living room quality, Panel quality, Door quality, Corpus quality
Wood is an extremely individual natural product. That is why the mentioned qualities are neither standardized nor normed. In fact, every supplier (or distributor) determines his own regulations regarding length, dimension and quality. Sub-grades can also be different within the standard qualities.
Therefore, a quality-oriented company could just grade what could be named as the highest quality from supplier A as only medium quality. As, on top of that, every customer has its own wishes and requirements, the parcels are generally being inspected before the purchase or at least representative samples are being sent in order to agree on the quality with the customer.
What however has to be determined first is the exact number of veneer sheets, the dimensions of the bundles and the quantity of the entire parcel.
What seemed to be an almost incredible measurement and documentation work in the past is fully automatic today. Bundle by bundle the veneers move over photocells on a conveyor belt. They measure the exact width of the bundle on every centimeter, register and calculate these figures to a fair average width and record the length of each bundle. In our system, the square meter content of each bundle on account of its average width, length and number of sheets is calculated and saved or printed onto measurement lists.
But that’s not all: every single bundle is being photographed by a calibrated camera. The picture will then be saved together with all other bundle information into our merchandise management system. From there, it can be accessed on the push of a button and also electronically sent to prospective customers – for when time is short.
Would you like to know more about our manufacturing processes and learn all about our expertise in wood? Feel free to contact us.